Pass Six Sigma LSSGB Exam in First Attempt Guaranteed!
Get 100% Latest Exam Questions, Accurate & Verified Answers to Pass the Actual Exam!
30 Days Free Updates, Instant Download!
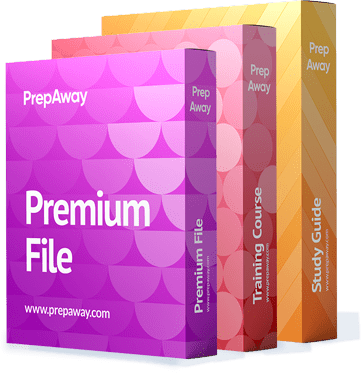
$39.99
LSSGB Premium Bundle
$69.98
$109.97
- Premium File 162 Questions & Answers. Last update: Jul 08, 2025
- Training Course 212 Video Lectures
- Study Guide 664 Pages
$109.97
$69.98
Last Week Results!

10
Customers Passed Six Sigma LSSGB Exam
Average Score In Actual Exam At Testing Centre
Questions came word for word from this dump
Get Unlimited Access to All Premium Files
Details
Purchase LSSGB Exam Training Products Individually
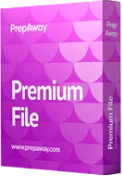
Premium File 162 Q&A
$65.99$59.99
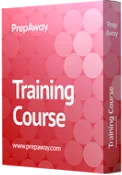
Training Course
212 Lectures
$27.49
$24.99
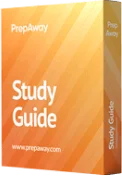
Study Guide
664 Pages
$27.49
$24.99
Why customers love us?
93%
Career Advancement Reports
92%
experienced career promotions, with an average salary increase of 53%
93%
mentioned that the mock exams were as beneficial as the real tests
97%
would recommend PrepAway to their colleagues